Comparison of brine transport
Comparative Test for the Transport of Brine with HDPE and Pexgol Pipes.
Case Study Nº
75
Customer
|
Working Conditions
Pexgol Pipes
Application
Lenght
Categories
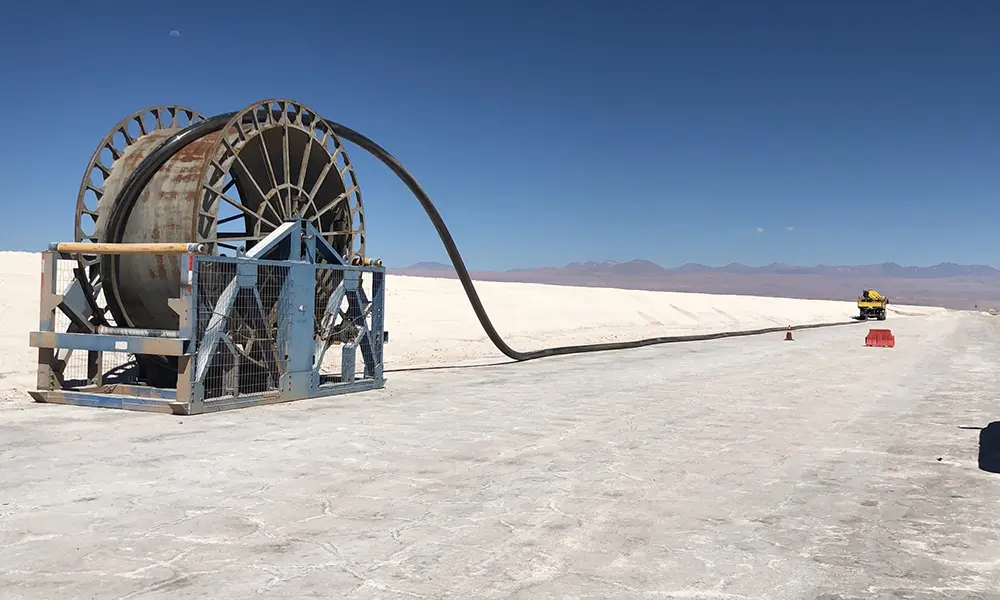
The Challenge
Albemarle salar decided to conduct a comparative test on their brine pipelines. The objective was to test the high resistance to scale formation that Pexgol pipes possess compared to conventional high-density polyethylene (HDPE) pipes.
Pexgol Solution
A Pexgol pipe was uncoiled by the main road from the salar to the parapet of 13D well, finally placing the pipe in the direction of 14D well to start the assembly according to its final disposition.
The flexibility of the Pexgol pipe allowed to fit easily into the layout, and its ability to be dragged greatly favored installation time.
Thanks to its high mechanical and impact resistance, Pexgol does not require the use of a special jacket.
For connection to the pump, a flanged coupling was used: clamp-type mechanical accessory with flange adjustment.
Pipe Type | Pexgol Cost vs Others | Pexgol Total Investment Costs vs Others |
---|---|---|
Rubbed steel A53 Gr, B Sch. 20 | 1:1.4 | 1:2 |
Stainless steel 316L, Sch. 20 | 1:2 | 1:3 |
Titanium B862, Gr.2, 3 mm thk | 1:2.3 | 1:3.2 |
Polypropylene PP-H, SDR 17 | 1:3.8 | 1:4.2 |
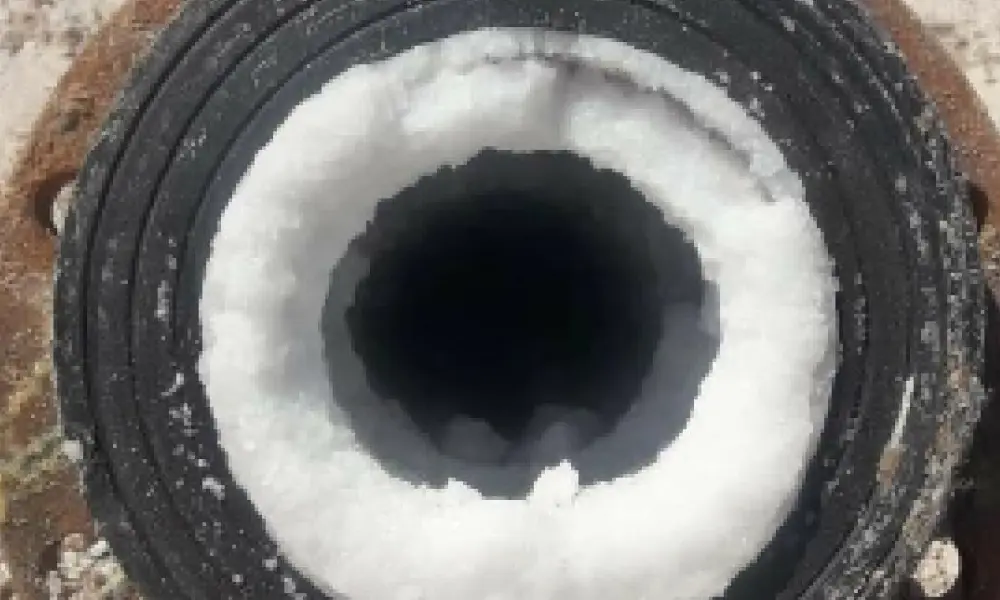
Sedimentation comparison: HDPE pipe after 30 days of use.
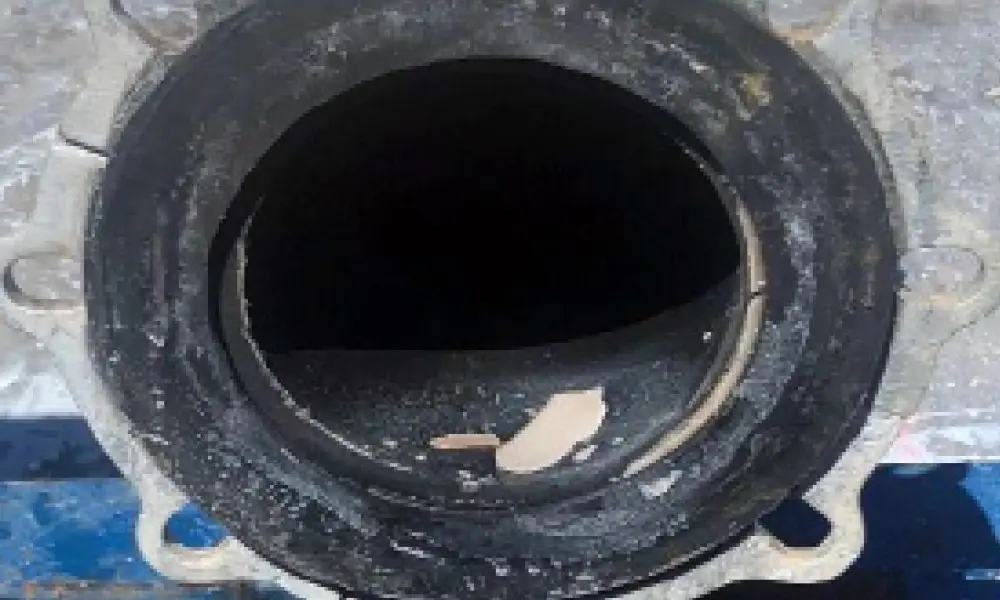
Sedimentation comparison: Pexgol pipe after 60 days of use.
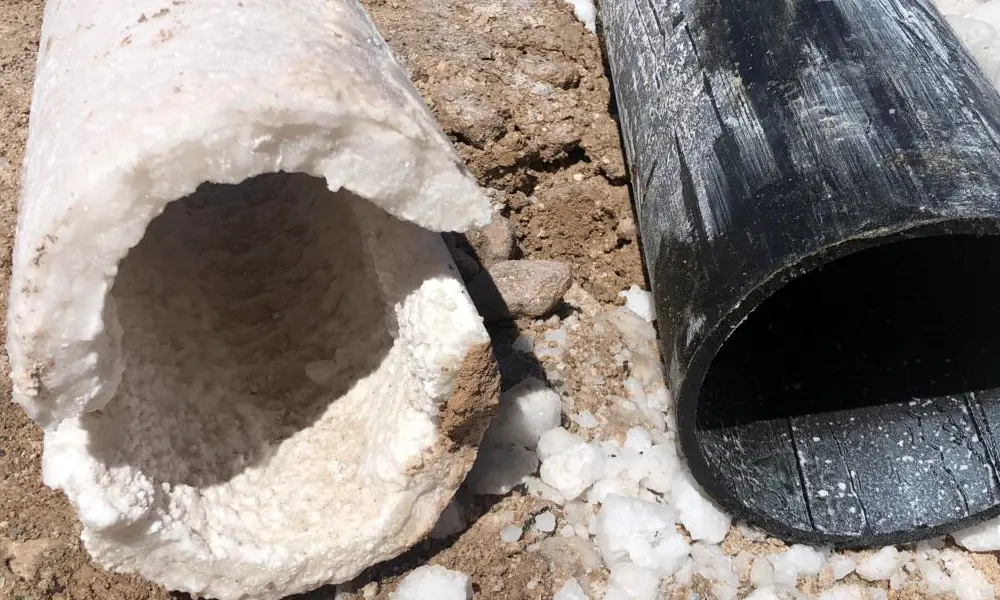
After 30 days of operation, the HDPE pipe has incrustations with an approximate thickness of 50 mm.
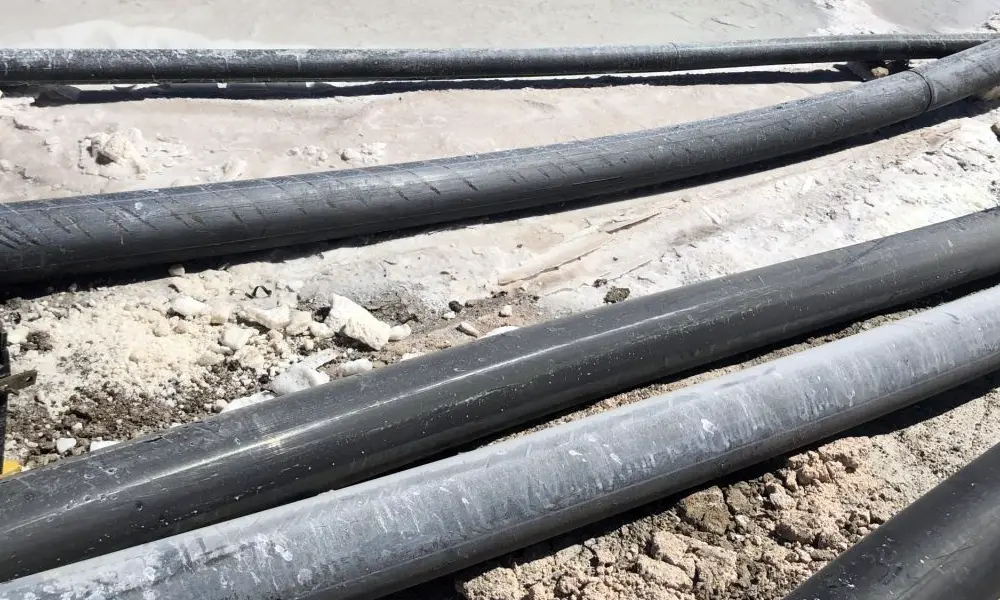
Cleaning HDPE pipes presents a great physical wear and tear for operators, as they must hit hard to loosen the scale, which means more hours spent on maintenance.
Related Case Studies
New Wastewater Treatment Plant with Pexgol Pipes
|
Mining Drainage Lines
|
Recovered Water Transportation
|